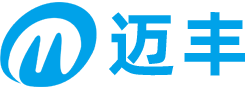
PVC發泡板生產中出現機械暗紋的問題,可能由多種因素導致,包括原材料質量、加工工藝、溫度控制等方面。針對這一問題,可以采取以下解決方法:
原因:原材料質量不合格是導致暗紋出現的一個重要原因。例如,PVC樹脂、發泡劑、穩定劑等關鍵原料的質量問題可能直接影響發泡板的品質。
措施:選擇質量穩定、符合生產要求的原材料供應商,并定期對原材料進行質量檢驗,確保原材料的質量滿足生產需求。
原因:加工工藝不當也是導致暗紋出現的一個重要因素。例如,擠出速度、螺桿轉速、模具溫度等工藝參數的設定不合理,都可能導致發泡板在生產過程中出現暗紋。
措施:
優化擠出工藝,調整擠出速度和螺桿轉速,確保物料在擠出過程中能夠充分熔融和塑化。
調整模具溫度,確保模具各部位溫度均勻,避免局部溫度過高或過低導致的暗紋問題。
定期檢查和維護模具,確保模具的精度和表面光潔度符合要求,減少因模具問題導致的暗紋。
原因:溫度控制不到位是導致發泡板出現暗紋的另一個重要原因。溫度過高或過低都會影響物料的流動性和固化速度,從而導致暗紋的產生。
措施:
采用先進的溫度控制系統,對擠出機、模具等關鍵部位進行精確的溫度控制。
定期檢查溫度傳感器的準確性和穩定性,確保溫度控制數據的準確性。
根據生產實際情況和物料特性,適時調整溫度控制參數,確保物料在適宜的溫度下進行加工。
原因:設備內部積聚的雜質和殘留物也可能導致發泡板在生產過程中出現暗紋。
措施:
定期對設備進行清理和維護,清除設備內部的雜質和殘留物。
檢查設備的密封性和潤滑情況,確保設備正常運行并減少因設備問題導致的暗紋。
原因:產品設計不合理也可能導致發泡板在生產過程中出現暗紋。例如,產品設計時未充分考慮材料的流動性和成型性。
措施:
在產品設計階段充分考慮材料的流動性和成型性,合理設計產品的結構和尺寸。
與生產部門密切溝通,確保產品設計符合生產實際需求和工藝要求。
綜上所述,針對PVC發泡板生產中出現機械暗紋的問題,可以從更換原材料、調整加工工藝、加強溫度控制、清理和維護設備以及改進產品設計等方面入手進行解決。通過采取這些措施,可以有效提高發泡板的生產質量并減少暗紋等質量問題的發生。