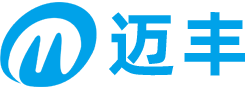
PVC發泡板表面起泡是一個常見的問題,可能由多種因素導致。以下是一些針對PVC發泡板表面起泡問題的解決方法:
控制擠出溫度:
熔體良好的塑化是PVC發泡板制品的前提條件。如果擠出溫度過高,容易發生熔體局部降解且會因熔體強度降低,氣泡過大而被撕裂;如果擠出溫度過低,熔體欠塑化、強度很低,同樣會出現破泡。
因此,需要設定和控制適當的擠出溫度,確保熔體在擠出過程中不發生降解,同時保證熔體強度。
選擇合適的樹脂:
采用粘度適宜的樹脂,有利于氣泡的分散與膨脹,以及板材整個橫截面壓力協調一致。
若PVC樹脂粘度過高,熔體流動性差,板面平整度難以保證,泡孔不易擴張,導致發泡倍率低;反之,若PVC樹脂粘度過低,又會致使熔體強度低,容易引發破泡。
合理添加發泡劑:
放熱型發泡劑發泡率高,分解速度快、放熱極大,但發泡時間短,突發性也強。因此當AC發泡劑用量過多時,發氣量過大,會使氣泡內壓力增長快,泡孔尺寸生長過大,急劇釋放氣體,使泡孔結構破壞,泡孔大小分布不均,乃至形成開孔結構,會在局部產生較大的氣泡和空穴。
在不影響發泡率前提下,可適當多添加吸熱型發泡劑,取代部分放熱型發泡劑,以抑制多添加放熱型發泡劑引發的破泡。
使用發泡調節劑:
發泡調節劑的長分子鏈纏繞粘附在PVC的分子鏈上,形成一定的網狀結構,一方面促進物料塑化,另一方面提高PVC熔體強度,使發泡過程中泡孔壁能夠承受泡孔內氣體的壓力,不致因為強度不足而破裂。
若發泡調節劑質量差或加量不足,會導致發泡體強度低,出現破泡或串泡。
穩定劑:
定期對穩定劑進行180~200度的穩定性能檢驗,不符合穩定性能要求的原料不得使用或經調整劑量,檢驗合格后再用。
穩定劑應根據采用樹脂的牌號進行調整,如果穩定劑加量過多或過少致使發泡劑分解溫度過低或過高,都不利于發泡。
碳酸鈣:
CaCO3加量太多時,雖然能形成更多氣泡核,但如果碳酸鈣加量過多或顆粒過大,活性不好,形成團聚,在樹脂中分散或與樹脂截面結合不好,導致熔體強度降低,熔體中氣泡擴展時容易產生破泡。
應嚴格控制碳酸鈣劑量、粒度與活性。當碳酸鈣加量過大時,發泡調節劑也應相應增加。
潤滑劑:
潤滑劑分為外潤滑劑和內潤滑劑。外滑有利于脫模,對板材表面的光潔性有好處;內滑有利于塑化和熔體的流動性。
外滑太少,擠出機5區溫度不易控制,易升溫,這會導致合流芯溫度高,板材中間出大泡、串泡、發黃等問題,板材表面也不光滑;外滑多,析出會變得嚴重。
內滑不足板面難以控制厚度,表現為板材中間厚兩邊薄;內滑多,易出現合流芯溫度高的現象。
模具檢查:
檢查模具設計是否合理,口模平直段長度和壓縮比是否根據制品厚度進行了正確選擇。
定期清理模具內的殘留物,避免影響熔體的流動和發泡效果。
設備維護:
定期對擠出機、合流芯等設備進行維護和保養,確保設備處于良好的工作狀態。
檢查設備的溫控裝置是否準確可靠,避免溫度控制不當導致的發泡問題。
混料均勻:
嚴格按照混料程序進行混料,確保混料均勻。
避免混料過程中混入雜質或再生料過多導致的問題。
操作規范:
操作人員應嚴格按照操作規程進行生產,避免因操作不當導致的發泡問題。
綜上所述,解決PVC發泡板表面起泡問題需要從多個方面入手,包括調整生產工藝、優化配方、檢查設備與維護以及注意其他相關事項。通過這些措施的綜合應用,可以有效地提高PVC發泡板的質量和生產效率。