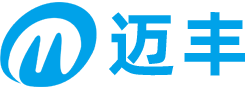
PVC發泡板從模具擠出時出現窩(即不平整、凹陷的部分)的問題,可能由多種因素導致。以下是一些可能的原因及相應的解決方法:
模具問題:
模具設計不合理,如排氣孔不足或位置不當,導致氣體無法順利排出。
模具溫度不均勻,導致材料在擠出過程中冷卻速度不一致,形成凹陷。
模具表面不平整或有損傷,影響擠出板的平整度。
工藝問題:
擠出溫度、壓力等參數設置不當,導致材料塑化不良或擠出速度不均勻。
冷卻系統不穩定,如冷卻水流量不足或溫度控制不準確,導致板材冷卻不均勻。
材料問題:
PVC樹脂與發泡劑的混合比例不當,或發泡劑分散性不好,導致發泡不均勻。
材料中含有雜質或水分,影響擠出效果。
優化模具設計:
增加模具排氣孔的數量和尺寸,確保氣體能夠順利排出。
檢查并調整模具溫度,確保模具表面溫度均勻。
定期清潔和維護模具,保持其表面平整和光滑。
調整工藝參數:
根據實際情況調整擠出溫度、壓力和速度等參數,確保材料能夠充分塑化并均勻擠出。
優化冷卻系統,確保冷卻水流量充足且溫度控制準確,避免板材冷卻不均勻。
控制材料質量:
選用高質量的PVC樹脂和發泡劑,并嚴格按照配比進行混合。
在使用前對材料進行干燥處理,去除其中的水分和雜質。
其他措施:
檢查并調整定型模與口模的對正情況,確保擠出板能夠順利進入定型模并保持直線前進。
定期檢查設備的運行狀態,確保設備正常運行并及時處理故障。
針對特定問題:
如果窩是由于材料在模具內局部過熱導致的,可以嘗試降低該區域的模具溫度或增加冷卻水量。
如果窩是由于材料在擠出過程中受到外力擠壓導致的,可以嘗試調整擠出機的螺桿轉速或增加擠出壓力的穩定性。
通過以上措施的實施,可以有效解決PVC發泡板從模具擠出時出現窩的問題,提高產品的質量和生產效率。