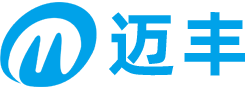
PVC發泡板出料不均可能由多種因素導致,主要包括以下幾個方面:
溫度過高或過低:擠出機的溫度設置直接影響原料的熔融狀態和流動性。溫度過高可能導致原料過度流動,而溫度過低則可能使原料流動性不足,進而影響出料的均勻性。
溫度分布不均:擠出機各區段的溫度分布不均也會導致出料不均。例如,某些區段溫度過高,而另一些區段溫度過低,使得原料在擠出過程中受熱不均,從而影響出料質量。
原料配比不當:PVC發泡板的原料包括聚氯乙烯樹脂、發泡劑、穩定劑、潤滑劑等,這些原料的配比直接影響產品的性能和質量。如果配比不當,如潤滑劑使用過多或過少,都可能導致出料不均。
助劑分散不充分:助劑在原料中的分散程度也會影響出料的均勻性。如果助劑分散不均勻,可能導致局部區域的原料性能差異,從而影響出料質量。
模具設計不合理:模具的設計直接決定了PVC發泡板的外形和尺寸。如果模具設計不合理,如模唇縫隙不均勻或阻流塊調節不當,都可能導致出料不均。
設備磨損或故障:擠出機、模具等設備的磨損或故障也可能導致出料不均。例如,螺桿磨損、模具堵塞等問題都可能影響原料的擠出效果。
操作不當:在生產過程中,如果操作不當,如牽引速度不穩定、切割時機掌握不好等,都可能導致出料不均。
管理不善:生產管理不善也可能導致出料不均。例如,原料混合不均勻、生產設備維護不及時等問題都可能影響產品質量。
針對以上原因,可以采取以下措施來解決PVC發泡板出料不均的問題:
調整擠出機溫度:根據原料特性和產品要求,合理設置擠出機的溫度,并確保各區段溫度分布均勻。
優化配方:根據實驗和生產經驗,調整原料的配比和助劑的用量,確保原料混合均勻且性能穩定。
改進模具設計:優化模具設計,確保模唇縫隙均勻且阻流塊調節合理。
加強設備管理:定期檢查和維護生產設備,確保設備處于良好狀態。
提高操作水平:加強員工培訓,提高操作技能和管理水平,確保生產過程穩定可控。
通過以上措施的實施,可以有效解決PVC發泡板出料不均的問題,提高產品質量和生產效率。