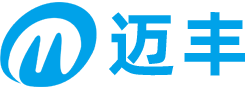
PVC共擠結皮發泡板的生產工藝是一個復雜而精細的過程,它結合了多種技術和設備,以確保最終產品的質量和性能。以下是該生產工藝的詳細步驟:
主要原料:包括PVC樹脂、發泡劑、穩定劑、潤滑劑等。這些原料需要按照一定比例進行精確稱量,以確保產品的性能和質量。
原料選擇:原料的選擇對產品的物理性能、化學穩定性和加工性能具有重要影響。因此,需要選用高質量的原料,并根據產品要求調整配比。
將稱量好的原料放入高速混合機中進行混合,使各種原料充分均勻混合。
混合過程中需要控制混合時間和混合溫度,以確保原料混合均勻且不會因過熱而分解。
混合好的原料通過錐雙螺桿擠出機進行擠出。擠出機是生產線的核心設備,其性能直接影響產品的質量和生產效率。
在擠出過程中,原料在高溫和高壓下被熔融并擠出成板材形狀。螺桿的轉速、擠出溫度等參數需要根據產品規格和原料特性進行調整。
擠出的板材在擠出機出口處進行發泡處理。發泡劑在板材中受熱分解產生氣體,使板材內部形成大量微細泡孔,從而實現發泡效果。
發泡過程中需要控制發泡劑的用量和發泡溫度,以確保發泡效果均勻且穩定。
發泡后的板材需要迅速通過冷卻定型裝置進行冷卻和定型。冷卻定型裝置通常采用水冷卻方式,通過快速降溫使板材固化并保持形狀穩定。
冷卻過程中需要控制冷卻速度和冷卻溫度,以避免板材變形或產生缺陷。
冷卻定型后的板材通過多膠輥牽引裝置進行牽引,以確保板材在后續加工過程中的穩定性和連續性。
牽引后的板材根據客戶需求進行切割,切割成不同長度和寬度的成品。
切割后的成品需要進行質量檢驗,包括外觀檢查、尺寸測量和性能測試等。合格的成品將進行包裝和入庫,供后續使用。
模頭設計:根據生產工藝和模頭的不同,PVC結皮發泡板可以分為模內雙流道模頭生產的塞盧卡結皮發泡板(向內發泡)和單流道模頭生產的結皮發泡板(向外發泡)。模頭的優化設計可以消除物料在模腔中的掛料、積料現象,提高制品表面的光潔度和質量。
工藝參數調整:螺桿轉速、熔體溫度、擠出壓力及機頭、口模、冷卻定型模結構等多種因素都會影響PVC結皮發泡板材的質量。因此,在生產過程中需要根據實際情況調整這些工藝參數以獲得最佳的產品性能。
整個生產過程高度自動化,減少了人工操作環節,提高了生產效率和產品質量。
采用先進的錐雙螺桿擠出機和冷卻定型裝置等設備,確保了產品的穩定性和一致性。
綜上所述,PVC共擠結皮發泡板的生產工藝是一個復雜而精細的過程,需要嚴格控制各個環節的工藝參數和設備性能以確保最終產品的質量和性能。